STLs and 3D Printing for PolyJet

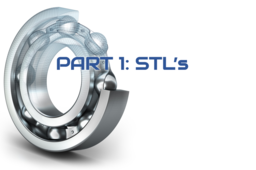
This tutorial is the first part of our series about how to prepare and optimize settings for mesh file types supported by GrabCAD Print (GCP).
The tutorial explains the building blocks of 3D printing with PolyJet. We will explain the conversion process from a CAD file to an STL file and how to optimize it to achieve the best print results possible. Future tutorials in this series will then explain more advanced types of files and operations.
-
Step 1: From CAD to STL
How the conversion works
All 3D files originate in CAD programs, a combination of hardware and software that enables engineers and architects to design everything from furniture to airplanes. After designing a model in a CAD program, you save the design in a format that the 3D printing software can read, the most common of these is called Standard Triangulation Language (STL) file.
STL files are the key to translating 2D designs made on a computer into 3D prints. The STL file approximates the surfaces of the converted CAD model with triangles. The number and size of the triangles determine how accurately curved surfaces are printed. So, the more complex the original CAD model geometry, the more triangles it will have to represent those features.
Why we need to convert
GrabCAD Print can read and automatically convert from native CAD. However, if the file type is not supported by GCP, there are software packages that will export file types not currently supported by Grab CAD, such as FBX. These packages will typically be able to export a file that can be imported into GCP such as STL, VRML, and OBJ.
For CAD-designed models that need to be converted to an STL file, the STL file type describes only the surface geometry of a three-dimensional object with triangulated surfaces. This file type does not store information relating to texture or color. There are other types of printing files that developed after STLs that do store information regarding color and texture, such as VRMLs and OBJs. We will cover them in our next tutorial.
Understanding the quality/size trade-off:
The difference between a high quality STL and a “bad”, lower-quality, possibly faceted model is the number and size of the triangles the STL uses to replicate the geometry represented by the CAD design. More, smaller triangles will fill in the gaps better and render a more accurate conversion. The more complex the surface, the more triangles your CAD file should generate for an accurate representation.
This image shows that flat surfaces can use fewer triangles while a more organic, complex shape like a cylinder needs more, smaller triangles.
At the same time, the more triangles the STL file has, the larger the file size. So, when creating an STL file, the goal is to achieve a balance between file size and a fully-defined model that accurately represents smooth curved geometries.
-
Step 2: Optimizing STLs for Best Results
There are three main considerations for best results in STL files:
a) Resolution
b) Angular tolerance
c) Storage format
Resolution
As we mentioned above, the quality of the printed part is defined by the density of the triangle mesh. The resolution setting is what determines that density. Higher resolutions create more triangles and greater accuracy, but also heavier files. Choose a resolution that balances reasonable file size and a fully-defined model with smooth, curved geometries.
More complicated geometries will necessitate more triangles, more resolution, and heavier files. We illustrate this point below:
For a simple model such as a box, surfaces can be approximated with twelve triangles.
But the more complex the surface, the more triangles produced.
A mesh resolution of 0.005 millimetres generally produces a good quality STL file. A resolution of 0.001mm may be required for certain geometries to ensure capturing high accuracy and design intent. Reducing mesh resolution below 0.001mm does not necessarily mean that model accuracy is improved.
We recommend that:
• you create large parts or highly detailed parts with a higher resolution than small
parts.
• you use double the resolution of the printer for intricate parts with many contours or curved surfaces.
For example, on the J750 3D printer the following mesh resolution is recommended:
· When Printing in High Quality: 0.007mm
· When Printing in High Mix: 0.0135mm
It is worth noting that these settings may not be achievable with all CAD software packages. Each software has its own structure, settings, capabilities, interface, etc.
To conclude, a final rule of thumb for setting resolution: If the STL model appears coarse and faceted on screen, you will see it in the finished model. The printed part will not print any better or smoother than the STL.
Angular Tolerance, Chord Tolerance, Deviation
Resolution is not the only setting you can manipulate to control the quality of your CAD model during conversion to STL. When exporting a CAD model to STL, the number and size of the triangles can be controlled along with other functions of the triangles formation, by adjusting the appropriate tolerance parameters. These settings have a major effect on the quality of the STL output in terms of replicating the design intent accurately.
Each printing software will have its own version of these tolerance settings and its own terminology. In this case, we will look at the settings in SolidWorks®.
• Chord Tolerance/Deviation—
This parameter specifies the maximum distance between a chord and the part's surface
(see figure below). It controls the degree of tessellation on the model surface (that is, the number of triangles on the model surface). A smaller chord height will result in a more accurate curvature of the surface, but a larger file.
• Angular Tolerance—
This parameter regulates how much additional tessellation occurs along surfaces with
small radii. The smaller the radii, the more triangles that are used.
Overall, these settings control the maximum distance allowed between the edge of a facet and the
actual surface of the designed CAD model.
The effect of changing the chord deviation parameter during STL generation is shown below:
Storage Format
There are two storage formats for STL files:
• Binary (recommended)—
A computer-readable file (non-text file). Each character position can hold any one of 256
different binary codes.
• ASCII—
A human-readable text file. This generates a large size file that is impractical to work with and errors may occur when working with assemblies
-
Step 3: Fixing STL files
Sometimes the file does not translate optimally, resulting in certain unsustainable features that need to be corrected. When GrabCAD Print automatically converts models from CAD to STL, it checks and repairs any errors on the imported models. But take special care when using the automatic fix operation in GrabCAD Print, as the algorithm can make changes to the model that may result deviations from design intent.
If that happens, you can use a third-party STL fixing software package, such as Materialise™ Magics™ or Autodesk® NetFabb® to identify and repair problems in the geometric structure with more precision.
That concludes our first deep-dive tutorial on optimizing file settings for 3D printing. Our next tutorial will talk about other, more advanced file types beyond STL.