How to Work with Colors & Procedural Textures in KeyShot & GrabCAD Print

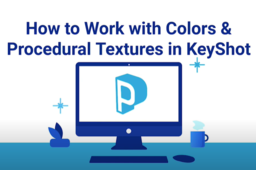
Creating actual 3D depth and physical textures on your 3D models is one of the first steps to designing a realistic prototype that looks and feels how you want it to. In this tutorial, we’ll explain how to work with procedural textures in KeyShot before you 3D print it using.
-
Step 1: Import your part file
Import your SOLIDWORKS part of your choice! This part came from Siemens NX then converted to a step file in SOLIDWORKS.
-
Step 2: Select the procedural texture you want
- Within the KeyShot Materials Library, scroll down to the material of your choice (wood in this case)
- Select procedural
- Then simply drag and drop the material selection onto the body that needs it.
Fun fact: Procedural textures allow for unlimited resolution while still being storage friendly.
-
Step 3: Customize your texture
Moving to the KeyShot Materials Menu, selecting textures allows for the customization of the texture that has been applied to the body.
(For this video, manipulation of the center z slider alters where the wooden rings lie on the frame of the glasses!)
Selecting the handle, we move back to the KeyShot materials library to select the clear rough plastic. Like the wood texture, all we need to do is select the material then drag it onto this specific body.
-
Step 4: Customize transparency and color
Once applied, we refocus on the KeyShot materials menu. We stay on the properties tab because we want to alter the overall transparency and color (this is the diffuse setting) rather than the specific placement.
It is important to alter this setting because we are working with a 3D model that will be printed rather than just a 3D render we would only see in a simulated environment.
-
Step 5: Select surface finish and look
We apply our final material (paint gloss white) onto the hole of the handle.
We move into the materials graph to establish the relationships between color, material, the texture. We first add a “brushed” box because that is the tactile feel we want.
We then connect that to the node labeled bump in the paint box so that the color reflects that texture. We conclude the use of the materials graph by connecting the paint box to the surface part of the Materials box so that both the color and texture are shown in the material we chose.
-
Step 6: Consider design realism best practices
In the demo video above, you’ll notice the designer plays around with the colors. He’s doing this because he’s trying to decide which color shows the contrast of the regular wood and wooden rings -- to make it look as realistic as possible.
For instance, decreasing the spacing of the rings allows for more rings in the spoon.
- Fun fact: Tree rings correspond to the amount of years the tree has been alive. Decreasing ring noise gives the wood a smoother look.
-
Step 7: Export your part
- File
- Click on export
- Select 3MF! DPI (Dots per inch) is the resolution. 300 dpi is a good minimum for 3d printed parts, any lower and the file might be blurry.
-
Step 8: Open GrabCAD Print
We can open up GrabCAD Print and import our newly created KeyShot 3MF part. Notice how we have all our part’s bodies nice and separated from the start of our workflow!
We can even open Model settings in GrabCAD Print, and manipulate the transparency one last time on the tray. This is a major benefit for designers who want to make last-minute fixes.
3D printing tip: Be sure to change the orientation to maximise the print quality, reduce printing time, and to reduce the overall support material usage.
And don’t forget to change the finish to matte because wood is typically matte not shiny!