Tutorials on Injection Mould Designing

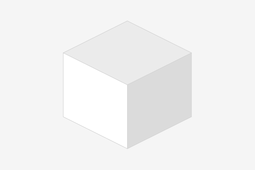
Today the topic is "FLOW SYSTEM"
No slide just Theory only, I will upload the slide soon.
Thanks and Enjoy..!!
-
Step 1:
Flow system: The design of a flow system to inject molten alloy in to a die cavity greatly influences the success of a die. The failure of many dies can be traced to faulty design of the flow system. By applying the basic principles of hydraulics a proper molten metal flow system can be developed.
The system aims at an efficient controlled delivery of through the flow system to the die-casting with mixing of molten alloy and air.
Machine suitability:
Choice of suitable machine is important aspect of die designing. Two main consideration determine suitability:
Clamping force.
Injection capability. -
Step 2:
Clamping force can be calculated by multiplying the projected area of the impression including runners,gate overflow by the injection pressure.The result should be less than the clamping force of the machine. The injection capability or metal pumping capacity of the machine must be determined from the pQ2 diagram.
The flow system comprises of a series of passage of varying lengths and diameters which carry molten alloy at varying high velocities from the under side of the injection plunger to the gate.
The flow system should be properly designed and manufactured to minimize the energy losses.
The flow system should converge from gooseneck to gate, sharp corners should be avoided and the surface of the flow path should smooth and well finished. -
Step 3:
The sprue:
The sprue has two basic functions:
1. To provide a smooth flow path between nozzle and runner.
.
2.To provide a means of rapidly solidifying molten metal alloy at the entrance of the die after the cavity has filled and the flow has stopped.
3.Runner type sprues have been developed to achieve a smooth flow path with uniform cross section, minimum change of direction and smooth transmission from nozzle to sprue and sprue to runner. -
Step 4:
The runner system from sprue to gate:
Main runner:The main runner join the sprue to the final tapered tangential runners feeding the gate. They should be as shot as possible and must have a constant cross sectional area.
Tapered tangential runners:
Tapered tangential runners provide the final flow path from main runners to gate. They provide an efficient flow path based on simple geometry and permit the use of the very thin gates (from 0.15-0.3mm). -
Step 5:
Runner cross section:
Circular sections give best flow efficiency and minimize thermal losses, but are the least practical cross section from the tool makers view.
For tapered tangential runners modified square or trapezoidal shapes are used. Area calculations are based on square sections and are converted into trapezoidal shapes.
Pairs of tapered tangential runners can be used to feed a long gate into a single cavity.A thin delta shaped region between the paired runners is found. -
Step 6:
Shock Absorbers:
The small ends of tapered tangential runners terminates in simple disk shaped shock absorbers. The control the very high transient velocities which may occur at the small ends of the runner. Shock absorbers also protect the die when the does not flow completely as in the case of a cold die during setup,when very high velocities can be reached.
Fan Gate:
Correct design and dimensions of gates is essential to achieve high casting quality and efficiency. The fan gate has been largely superceded by by the tapered tangential runner. To increase its efficiency the inlet should be larger than the gate. -
Step 7:
Gate Positioning
General guidelines for gate positioning:
Center gating: Center gating offers the best feeding configuration. It permits the use of short direct feed system. It achieves an ideal flow path across the die cavity.
Edge gating susing tapered tangential runners:
The following are the recommendations :
The longest uninterrupted length of casting available for casting should be choose but it must satisfy the shortest and smoothest flow path across the cavity.
The direction of metal flow in the cavity sho9uld be chosen such that at least one side or corner be open during fill time to allow for venting. -
Step 8:
Gate area:
The total gate area must always be smaller than nozzle exit area. But its should not be less than 40% of nozzle exit area.
Gate velocity:
The velocity of molten alloy through the gate depends on :
The energy of machine
The pressure losses in the total flow system in the gate.
The type of runner.
True velocity through gates fed by tapered tangential runners is higher than the figure arrived at using the formula:
Velocity(v) = volume flow rate(Q)
gate area(A) -
Step 9:
Air vents:
The use of converging flow system with correctly designed runners ensures that air in the feed system is pushed out a head of the molten alloy flow and expelled through the cavity trough the air vents.
Depth greater than 0.075mm will lead to flashing problem.
Overflows: No over flows need be cut prior to the first casting trial unless their use is specified for ejection purpose. On trial if the castings exhibit poor finish or blister the following conditions must be checked first:
Machine operations and performance
Feed system design and performance.
This will establish both machine and die are operating at the design parameters. -
Step 10:
Thanks..!!!